新規製作した金型にはトラブルがつきものです。この記事では試作時に発生しやすいトラブルと対策を紹介します。
試作時に発生しやすいトラブル
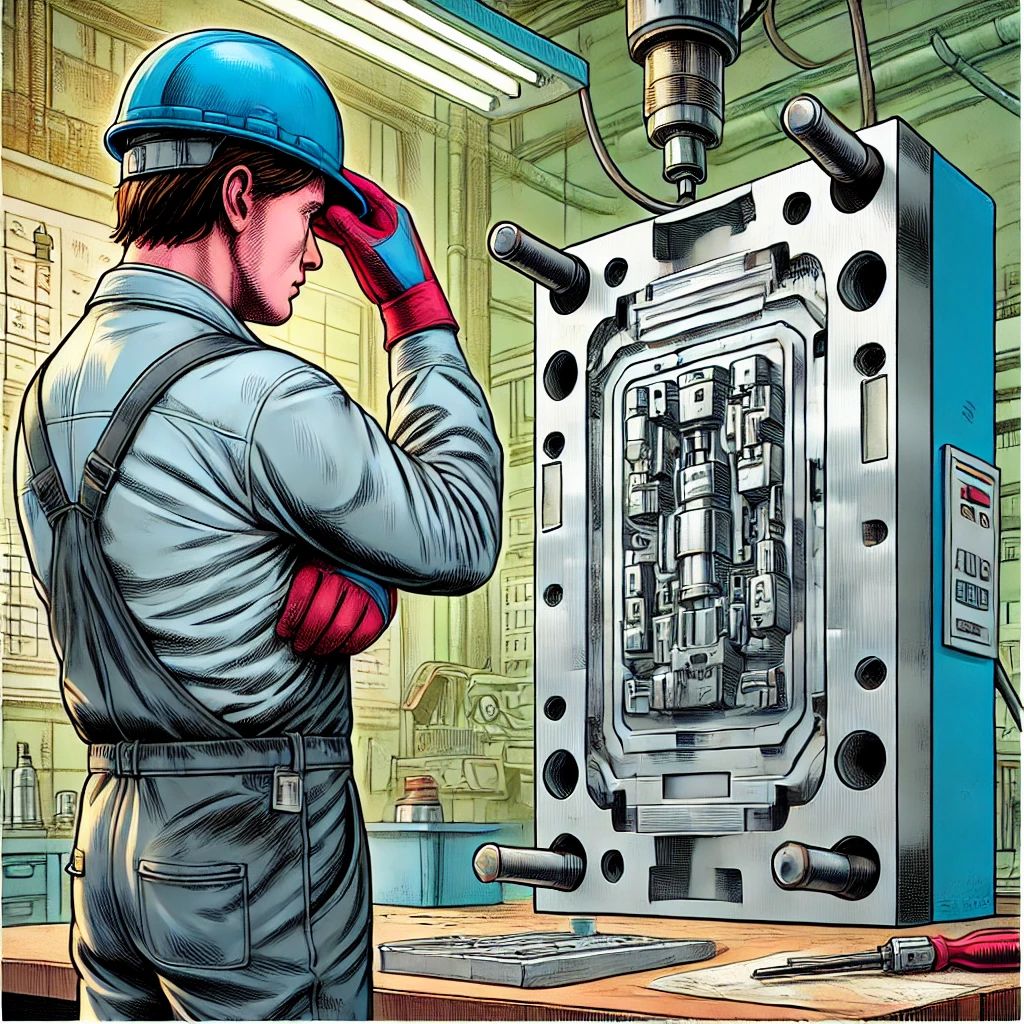
金型破損
成形不良
不良現象 | 不良内容 |
バリ | 金型の隙間から樹脂が漏れ出し、製品のエッジに不要な薄い膜や突起ができる成形不良。 |
ショートショット | 樹脂の充填不足により成形品の一部が未形成になる不良で、低圧力や低温、ガス詰まりが主な原因。 |
ウエルドライン | 樹脂の流れが合流する際に発生する線状の痕で、強度低下や外観不良の原因となる成形不良。 |
シルバー | 樹脂内の水分やガスが急激に膨張し、成形品表面に銀色や白っぽい筋状の模様が発生する不良現象。 |
ヒケ | 樹脂の冷却・収縮によって成形品表面が凹む不良で、肉厚部やボス周辺に発生しやすい。 |
糸引き | 射出成形時にゲートやノズルから溶融樹脂が細い糸状に引き伸ばされ、製品に付着する不良現象。 |
ゲート残り | 成形後にゲート部分の樹脂が適切に切断されず、製品に突起や跡が残る不良現象。 |
黒点 | 異物混入や分解した樹脂の影響で成形品表面に発生する黒い斑点状の不良。 |
ジェッティング | 樹脂が高速で射出されることで発生し、成形品表面に蛇行した流れ跡が残る不良現象。 |
フローマーク | 樹脂の流れのムラによって製品表面に生じる模様や筋 |
反り | 冷却不均一や残留応力により成形品が変形する現象 |
クラック | 成形時の応力集中や冷却不良による亀裂 |
各トラブルへの対策
- 設計段階での強度解析を実施
- 適切な材料選択
- 流動解析によるシミュレーション
まとめ
試作時のトラブルは事前の設計や条件設定で大部分を回避できます。しかし、実際に試作をすることで見えてくる問題もあります。迅速に原因を特定し、適切な対策を講じることで、量産時の安定性を確保できます。
コメント